Altilium ups the ante on lithium recycling, CAM production from lithium scrap
British firm Altilium has claimed progress in its 'EcoCathode' hydrometallurgical recycling technology, with breakthroughs in the recovery of lithium from new battery chemistries and the production of cathode active materials (CAM) from a mixed feed of lithium scrap.
Claimed as the only company in the United Kingdom involved in the recycling and upcycling old EV batteries to high nickel P-CAM and CAM for direct reuse in new batteries, the company is attempting to develop a sustainable battery raw materials supply chain in the country and cut its dependence on China.
Altilium's proprietary 'EcoCathode' process has claimed successfully processing of LFP batteries, recovering over 97 percent of the lithium at high efficiency. Further, the company has also delivered the latest generation of its CAM, recovered from old NMC111 battery chemistries and production scrap.
Now, for the first time Altilium has produced an advanced NMC 622 high nickel chemistry from a mixed stream of lithium scrap. Using the EcoCathode process, Altilium's latest generation CAM has the potential to extend the lifespan of new batteries, with 60 percent reduction in carbon emissions and 20 percent cut in costs as against virgin raw material.

Altilium partners with Nissan for EV battery recycling project in UK
Having demonstrated its ability to recycle both LFP and NMC batteries, Altilium's first mega-scale recycling facility to be located in Teesside, has been designed to process a mixed feed of battery chemistries, including LFP.
Christian Marston, COO of the company, commented on the development, "At Altilium we are committed to developing innovative new technologies as we look to build a domestic supply chain for the lowest carbon battery materials. By optimizing our technology we are resolving some of the economic challenges around recycling LFP batteries and also demonstrating our ability produce high quality CAM."
Altilium is also able to recycle the graphite, for reuse in the production of new anodes. While the iron and phosphate are less valuable, they can still be recovered for reuse in other industries, according to the company.
With its recycling into CAM, the company will be able to offer a closed loop solution to OEMs and cell manufacturers, with EV battery collection from the final holder, processing of waste batteries and chemical refining to battery-ready, sustainable materials for direct reuse in the production of new batteries.
Altilium's Teesside recycling plant is expected to produce about 30,000 tonnes of CAM per year, well enough to support about 20 percent of new EVs produced in the UK by 2030.
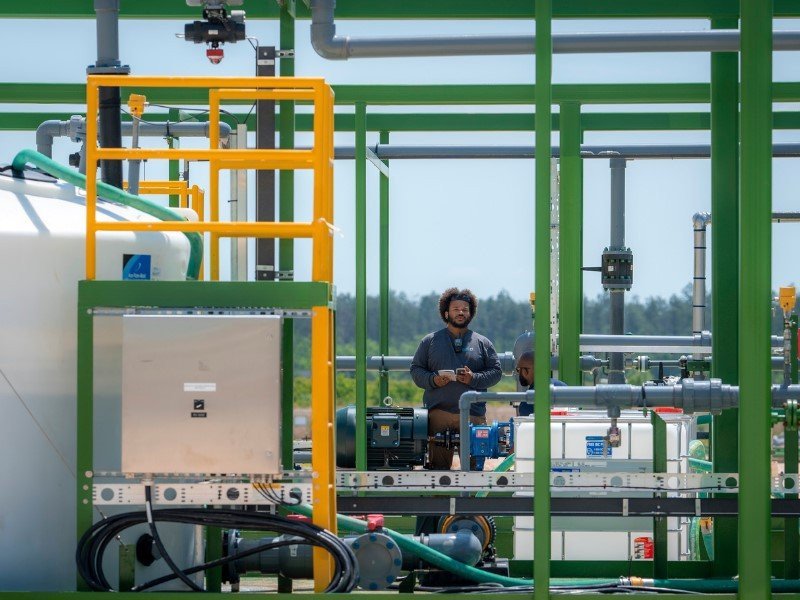