Taking a look at the mushrooming of mega-sized battery cell manufacturing plants: why JVs between auto OEMs and cell makers can secure steady demand, but also why it makes sense for cell makers to explore a wider market. Taking the Tesla-Panasonic partnership as a case-in-point, Akash Saraf, Sr. Analyst - Emerging Technologies, CES, explores the way of the 'giga' trend.
In July 2022, Panasonic, together with Kansas Governor Laura Kelly, announced an agreement related to the location of the company's new US lithium-ion battery cell factory. The Japanese company intends to build the plant in De Soto, Kansas, investing $4 billion and create up to 4,000 new jobs.
Reading about this new development, one of the few questions that come to mind is: why is Panasonic building a separate Giga factory in Kansas, when it could expand the current Gigafactory in Nevada, which is jointly operated by Tesla? Before getting to the answer, let us understand a bit about the Tesla and Panasonic partnership.
Technically Panasonic could sell these batteries to other manufacturers; however, the contract between the two companies gives Tesla the first right of refusal on all battery supplies. Tesla has exclusive rights to all batteries produced there and unless it refuses, Panasonic can't sell to other auto manufacturers.
Reading about this new development, one of the few questions that come to mind is: why is Panasonic building a separate Giga factory in Kansas, when it could expand the current Gigafactory in Nevada, which is jointly operated by Tesla? Before getting to the answer, let us understand a bit about the Tesla and Panasonic partnership.
- Tesla's first three vehicles use 18650 cells sourced from Panasonic, for Model 3 – Tesla then went with a larger format - 2170 developed by Panasonic at the Nevada Gigafactory
- Tesla owns the factory building itself and leases the battery manufacturing part of the premises to Panasonic
- Panasonic owns and operates the machinery, turns it around, and sells the output to Tesla.
Technically Panasonic could sell these batteries to other manufacturers; however, the contract between the two companies gives Tesla the first right of refusal on all battery supplies. Tesla has exclusive rights to all batteries produced there and unless it refuses, Panasonic can't sell to other auto manufacturers.
While the arrangement suits Panasonic (as it has a ready built-in customer in Tesla), it does put the battery maker in a twist as it has put all the manufacturing investments in the production agreement with Tesla. It is a cost-plus contract, with price-to-sales profit and margins based on meeting Tesla's expectations and goals, where Tesla has control over how much it can make from battery manufacturing operation at the Nevada Gigafactory.
Panasonic remains strong with the agreement and will continue making batteries in Nevada. It has maintained its market share in the lithium-ion battery market almost exclusively through its relationship with Tesla. But as Tesla begins diversifying its cell sourcing, from suppliers other than Panasonic (LFP prismatic from CATL), it becomes imperative that Panasonic also look at other consumers of batteries if it wants to maintain its market share.
Panasonic remains strong with the agreement and will continue making batteries in Nevada. It has maintained its market share in the lithium-ion battery market almost exclusively through its relationship with Tesla. But as Tesla begins diversifying its cell sourcing, from suppliers other than Panasonic (LFP prismatic from CATL), it becomes imperative that Panasonic also look at other consumers of batteries if it wants to maintain its market share.
Here's why it makes sense for Panasonic to want to build its Giga factory.
This configuration has maxed out the space, and would require additional space to install new production lines, which will involve an expensive buildout of the factory, however, they could improve output by improving some of the older lines.
- Nevada Gigafactory has 14 manufacturing lines, with about 5.8 million 2170 format cells a day or over 2 billion 2170 format cells produced a year (~40GWh output).
- Lines 1-10: These are relatively older production lines with a production capacity of over 300k cells a day/line.
- Lines 11-14: These are more recently put in high-speed lines with over 600k cells a day/line.
This configuration has maxed out the space, and would require additional space to install new production lines, which will involve an expensive buildout of the factory, however, they could improve output by improving some of the older lines.
Panasonic has also started production of the new 4680 format cell introduced by Tesla, and it won't be long before other cell manufacturers begin production of the format as well. Hence, to maintain its lead in the market, it would make sense for Panasonic to build its own line for the 4680 formats, to cater to not only Tesla but also other auto OEMs.
According to recent news reports, Tesla is finally planning an expansion of its Nevada Gigafactory after years of operating out of only 30 percent of its size. Idea was to optimize its current production capacity and focus on building new factories that would include vertically integrated EV production. The plan to extend the Nevada premises will bring its production output closer to the originally intended plan of about 105GWh of battery cells and of over 150Gwh of battery packs. While the construction timeline is not disclosed, it is presumed that it will be fast enough to keep pace with the slew of giga factories that are coming up around the world.
With the giga factory trend started by Tesla, there has been a spurt in construction of mega-sized cell manufacturing facilities worldwide, and not just in North America. We see major auto OEMs partnering with cell manufacturers to set up LIB giga factories to cater to their own emerging demand for upcoming range of EVs.
- General Motors has partnered with Korean cell manufacturing giant LG Energy Solution, to setup a JV - Ultium Cells. This partnership plans to setup four giga factories across the US. GM has plans for a capacity of 70-90 GWh by 2030, to meet the demand for its upcoming range of EVs; aiming for a larger space of play in the EV arena, currently dominated by Tesla.
- GM recently announced a huge $7 billion investment in facilities in Michigan, which would roll out EVs and batteries. It is a record single investment in the history of GM and goes on to indicate the company's faith in the present and future of battery-powered vehicles.
- Ford has partnered with Korean cell manufacturing company SK innovation, to form a JV – BlueOvalSK. The partnership has announced a $11.4 billion investment for setting up three giga factories across the US.
- Volkswagen also has plans to establish six giga factories that will produce cells with a total energy value of 240GWh (40GWh each. The Group recently set up a battery business unit named PowerCo and has started work on its first battery factory in Salzgitter, slated to start production of the VW unit cell from 2025.
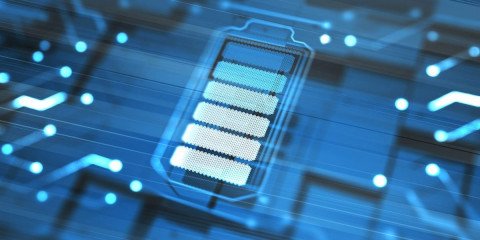
EBA calls for action to prevent battery investment outflows from Europe to US
In a recently held high-level meeting by European Battery Alliance (EBA) with European Commission Vice-President Šefčovič, the stakeholders discussed on the impact of the...
https://etn.news/buzz/european-battery-ecosystem-investment-outflows-actions
Read More