BMW Group has recently announced the rolling off the battery cell production line at its new Cell Manufacturing Competence Centre (CMCC) in Parsdorf, Germany. The samples of the cylindrical battery cells, similar to the ones that are likely to power the brand's 'Neue Klasse' vehicles from 2025 onwards, signifies the company's strident progress in battery cell technology and manufacturing.
The company claims that the CMCC in Parsdorf will enable it to span the whole cell value creation process with regard to cell manufacturing. With this know-how, the BMW Group is setting benchmarks for production, quality, performance, costs and environmental standards, which it is implementing in close cooperation with its partners for standard production of battery cells, it adds.
RELATED: BMW to use round battery cells from 2025, plans for six 20 GWh giga factories
"With the Cell Manufacturing Competence Centre, we are strengthening Germany's capacity for innovation," explained Milan Nedeljković, member of the Board of Management of BMW AG, responsible for Production. "In this way, we are making an important contribution to the quantum leap in technology in the Neue Klasse."
Frank Weber, member of the Board of Management of BMW AG, responsible for Development, commented, "Production of battery cell samples in Parsdorf marks the next logical step in our battery cell strategy".
"The Cell Manufacturing Competence Centre is the perfect complement to our existing Battery Cell Competence Centre in the north of Munich. Development takes place there, then we scale the best product towards a series process in Parsdorf. Thanks to cross-divisional collaboration, we are able to link product and process in a unique way", he added.
BMW claims that the cells, specially designed for the 'Neue Klasse' EV architecture, will significantly increase the vehicle range (of the top model) by up to 30 percent (as per WLTP standards). The come with a standard diameter of 46 mm and two different heights of 95 mm and 120 mm.
RELATED: BMW to add high-voltage batteries logistics centre at Plant Leipzig
Compared to the prismatic cells of the fifth BMW battery cell generation, the nickel content of the sixth-generation BMW round cells will be higher on the cathode side, while the cobalt content will be reduced. On the anode side, the silicon content will be increased. As a result, the cell's volumetric energy density will improve by more than 20 percent, the company says.
BMW Group also maintains that it is systematically pursuing other future milestones, such as the ramp-up of the sixth generation of BMW electric drive trains and development of all-solid-state batteries (ASSB), at its battery cell competence centers in Munich and Parsdorf.
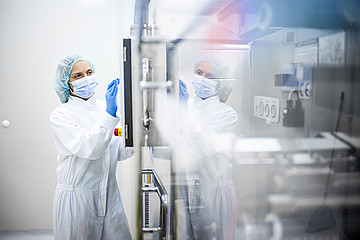
FEV opens lab for customized battery systems, cells in Germany
Read More