UK-based Altilium working on sustainable recycling of battery waste has announced a new collaborative project led by Nissan, which will see deployment of advanced recycling technologies to lower the carbon footprint of new batteries made in UK and reduce reliance on imported raw materials.
Building on Altilium's proprietary green processing technologies, the two companies will work together to maximize the potential for raw material recycling and develop a "closed-loop" model for battery materials, thus reducing the need for mining and saving natural resources.
This will include processing waste from used Nissan Leaf EV batteries and production scrap, which are to be upcycled to produce high nickel chemistry cathode active materials (CAM) for testing in the next generation of EV batteries.
The program is expected to strengthen the technical expertise and R&D capability of the Nissan Technical Centre Europe (NTCE) in Cranfield, Bedfordshire, focusing on the development and advancement of EV battery reuse, recycling and energy balancing technology.
The project is part of a £30 million collaborative project announcedby the Advanced Propulsion Centre (APC) with an awarded grant funding of £15 million. The collaboration also involves battery manufacturer and Nissan's supplier AESC and second-life battery energy storage solutions firm Connected Energy.
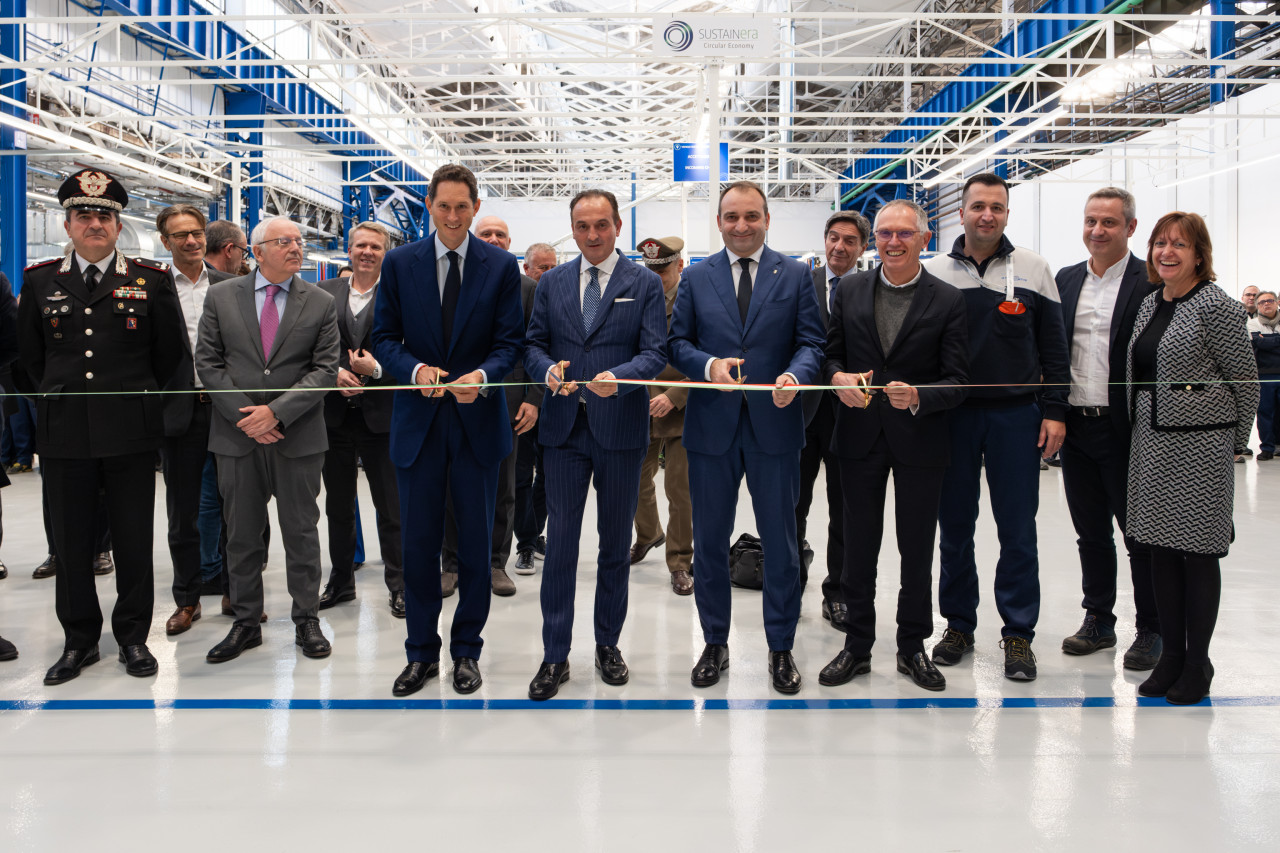
Stellantis opens Circular Economy Hub to recycle and reuse old EVs, batteries
Dr Christian Marston, co-founder and COO of Altlium, commented on the development, "The collaboration with Nissan, AESC and Connected Energy marks a significant milestone in our mission to create a sustainable ecosystem for EV batteries".
"Together, we are leveraging our strengths and resources to revolutionise how we manage and repurpose EV batteries, ensuring the UK has a domestic and sustainable source of battery materials for low carbon transportation", he added.
Altilium claims that its proprietary 'EcoCathode' hydrometallurgical process can recover over 95 percent of the cathode metals, including lithium, from end-of-life EV batteries. These recovered materials are re-engineered and upcycled to high nickel CAM, ensuring their seamless integration into new batteries.
By upcycling these critical materials, the company aims to reduce the carbon footprint in CAM by 50 percent and the cost by 20 percent, compared to freshly mined materials.
Altilium's full battery circularity model is expected to provide a unique customer offering in the UK, encompassing zero carbon EV battery collection, black mass recycling and chemical refining to produce 30,000 MT of battery-ready CAM, enough to meet 20 percent of UK requirement by 2030, according to the company.
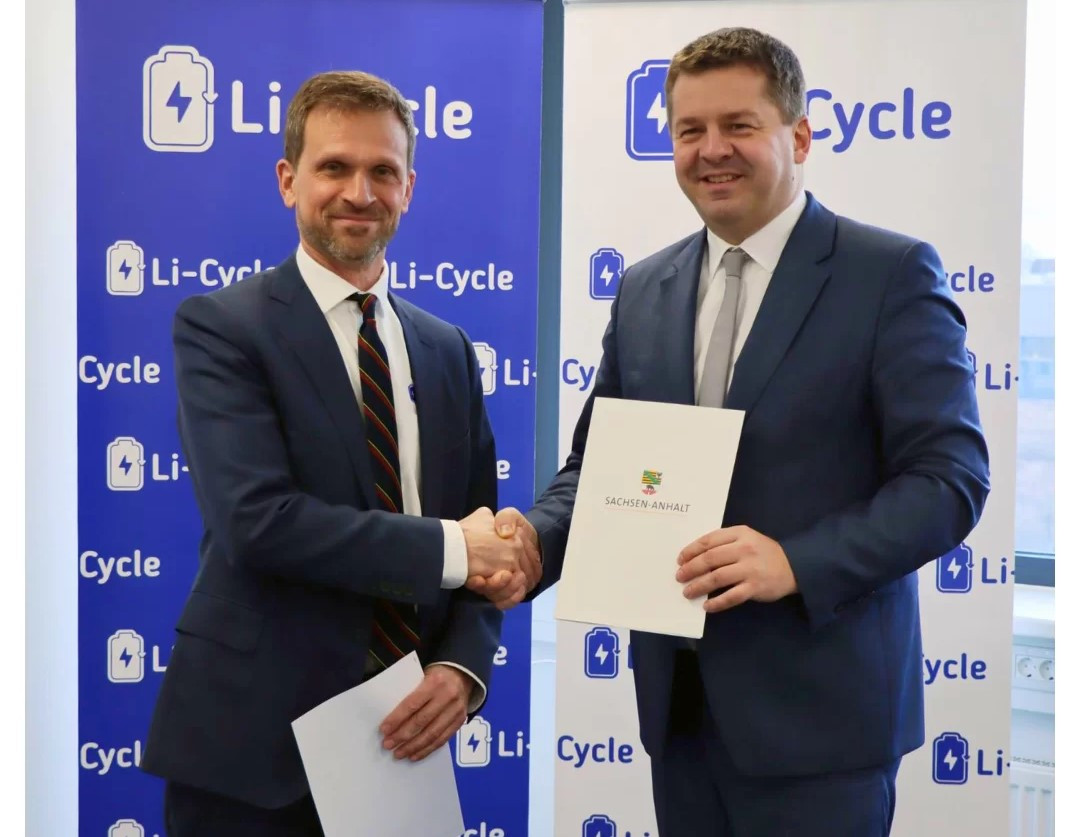
Li-Cycle bags €6.4 mn govt. grant for its lithium-ion battery recycling facility
Read More