VARTA-led 'ENTISE' project to develop next-gen sodium-ion battery technology
A consortium of 15 companies and universities researches led by battery firm VARTA acting as initiator and coordinator have announced their project named 'ENTISE'. It aims to develop industrially usable, high-performance and environmentally friendly cells using sodium-ion technology.
Sodium-ion batteries have the potential to redefine the future of sustainable and resource-saving energy storage in the coming years, as sodium is readily available, inexpensive, safe and can be easily disposed of or recycled. However, the challenge is to transfer this technology into industrially utilizable and scalable cells.
The ENTISE aims to develop a high-performance, cost-effective and environmentally friendly cell chemistry for sodium-ion batteries and to transfer it into functional cell formats that can be used in a variety of industries for end-use applications.
The project is being funded by the Federal Ministry of Research and Education with around € 7.5 million in grants. Rainer Hald, CTO of VARTA AG, commented on the project, "For the German battery community, this project represents a milestone in the development of sustainable sodium-ion batteries".
"In order to further advance the future of decentralized energy storage and use, other innovative and powerful storage technologies are needed in addition to lithium-ion technology. In addition to existing technologies, sodium-ion batteries can make an important, sustainable contribution to the decarbonization and electrification of many areas in order to actively shape the energy and mobility transition", he added.
The state funding of the project is an important sign that the R&D of cutting-edge technology in the battery sector can have a future in Germany and Europe, Hald noted.
Moreover, the ENTISE project focuses on the further development of existing material concepts and processes as well. From a technological perspective, the aim is to improve the storage capacities of the cathode and anode in particular. This involves optimizing the materials used, including the electrolytes.
Cycle stability, the ability to ensure stable cell performance even after repeated charging and discharging, is also to be improved by developing and using new materials, optimized electrode materials and coatings. A central component of the project will be the production of sufficient quantities of the necessary materials to build individual resilient laboratory samples through to prototypes in round cell design, according to the consortium.
In the final phase of the project, the individual components will be upscaled and transferred from the laboratory to the pre-industrial sector (piloting) in cooperation between the industrial and institute partners.
The final product of this upscaling will be a small series of round cells that will enable a reliable assessment of properties in practical application scenarios such as electric vehicles and stationary storage systems. The project partners have set mid-2027 as the timeline for the final phase of the project.
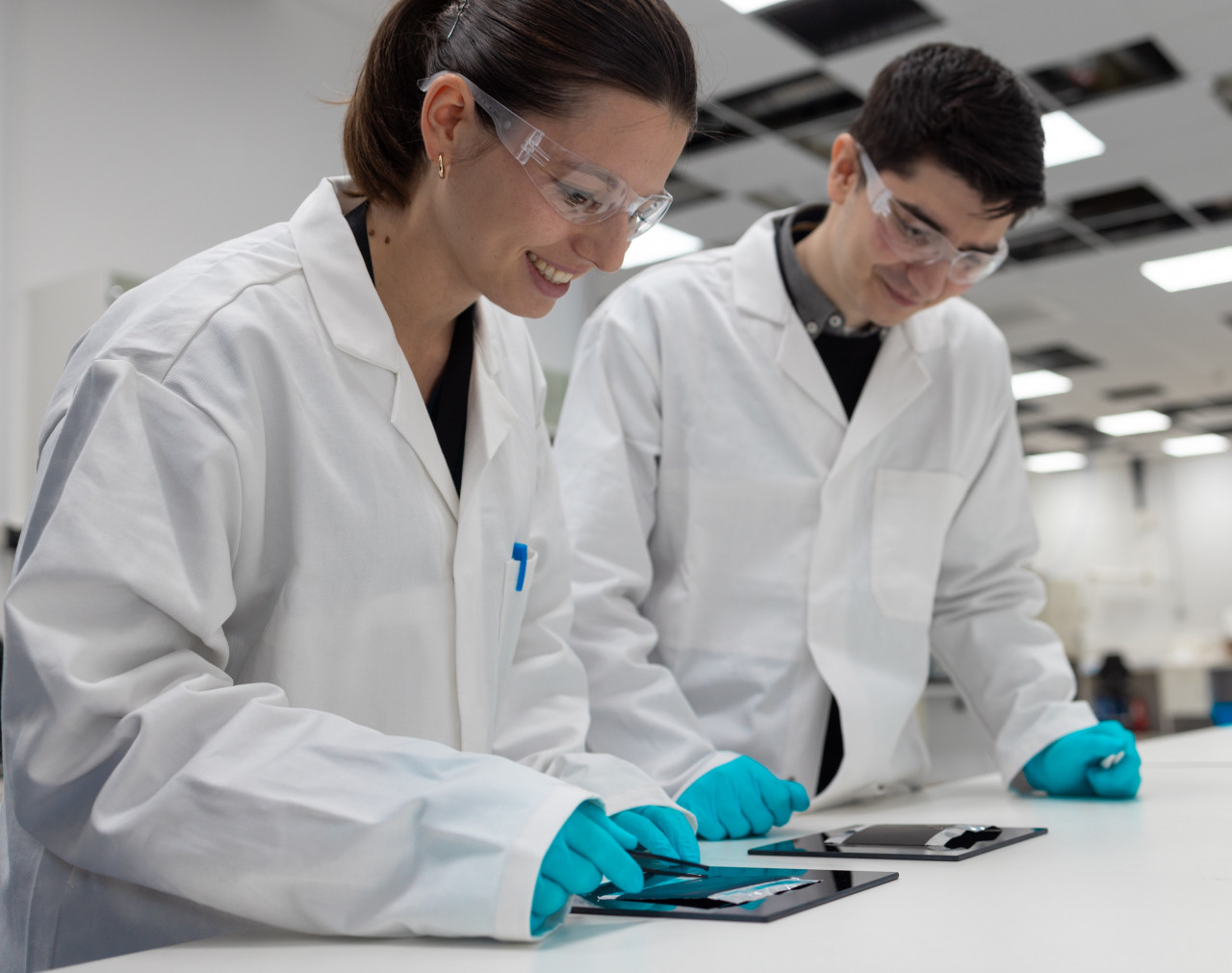