Electra recovers Lithium from Battery Recycling trial, claims improved economics
Canadian firm Electra Battery Materials Corporation had recently announced the successful recovery of lithium, a critical mineral needed for the electric vehicle battery supply chain, in its black mass recycling trial being conducted at its refinery north of Toronto.
The recovery and subsequent production of a technical-grade lithium carbonate product in a plant-scale setting validates Electra's proprietary hydrometallurgical process and efforts to date in commissioning its larger refinery complex, according to the company.
"Recovering lithium from black mass represents a potential game changer for Electra and the North American EV supply chain," said Trent Mell, CEO of Electra Battery Materials. "Recycling lithium from expired batteries through hydrometallurgy lowers the carbon footprint of manufacturing electric vehicles and represents an important source of future supply for a commodity whose demand is expected to grow significantly in the coming years. From Electra's perspective, it considerably strengthens the economics of our battery recycling strategy by providing another high-value product we can sell."
Mell further added, "Successfully demonstrating our lithium recovery process in a plant-scale environment supports our plans to commercialize our process with our industry partners and is a testament to efforts of Electra's technical team."
Black mass is the industry term used to describe the material remaining once expired lithium-ion batteries are shredded and all casings removed. Black mass contains high-value elements, including lithium, nickel, cobalt, manganese, copper, and graphite, that once recovered, can be recycled to produce new lithium-ion batteries.
"Our refinery team, combined with our consulting engineering partners, achieved a significant milestone in proving up our hydrometallurgical process for treating black mass," said Mark Trevisiol, Electra's Vice President of Project Development. "We achieved these outstanding results in less than two years, going from bench-scale laboratory testing to plant scale production", he added.
Established North American battery recyclers have focused on collecting and shredding of batteries with the resulting black mass material primarily treated by a pyrometallurgical smelting process that has a higher carbon footprint and lower metal recoveries than hydrometallurgical processes.
Recycling black mass will increasingly become a key feature of the EV battery supply chain given the strong demand for critical minerals and the looming supply deficit of metals such as nickel and cobalt. According to data from McKinsey & Company, available battery material for recycling is expected to grow by 20 percent per year through 2040, cites Electra.
The company launched its black mass demonstration plant at the end of December 2022, and has processed material in a batch mode, successfully extracting lithium, nickel, cobalt, manganese, copper, and graphite.
As Electra has decided to extend its black mass processing and recovery activities through June 2023, beyond the company's initial target of 75 tonnes, as a result of preliminary results achieved to date and interest expressed by potential commercial partners.
All of Electra's recovered material will be sold to third-party companies for additional processing and re-use in a number of applications.
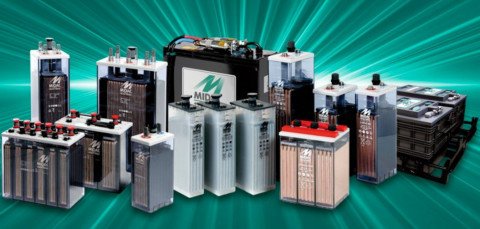